Traditional letterpress printing requires physical letters, cast from metal or carved from wood, which get inked and pressed into paper to make a print. In the last post, we took a look at the process of making type from metal (if you missed it, click here). In this installment, we’ll see how it’s created from wood.
Civil War recruitment poster.
From the International Printing Museum website.
http://www.printmuseum.org/museum/wood-type-2/
Wood came to be used as a material for making letters for printing primarily in the 1800s, when the printing and advertising industry became more widespread. Imagine trying to lift a big “Wanted”-poster-sized chase of metal type — pretty darn heavy! (See the photo of a Civil War recruitment poster.) Letters carved and routed from holly or maple were MUCH lighter, and could be made MUCH larger than their metal counterparts.
Here at the Press, we’re fortunate to care for and print with a nice selection of wood type, most of which was made between 1875 and 1910. If used with plenty of TLC, it’ll outlast us (just like our presses)!
Here's a slide-show of some of the materials and tools used to create wood type, along with some of the type in our collection here at the Press:
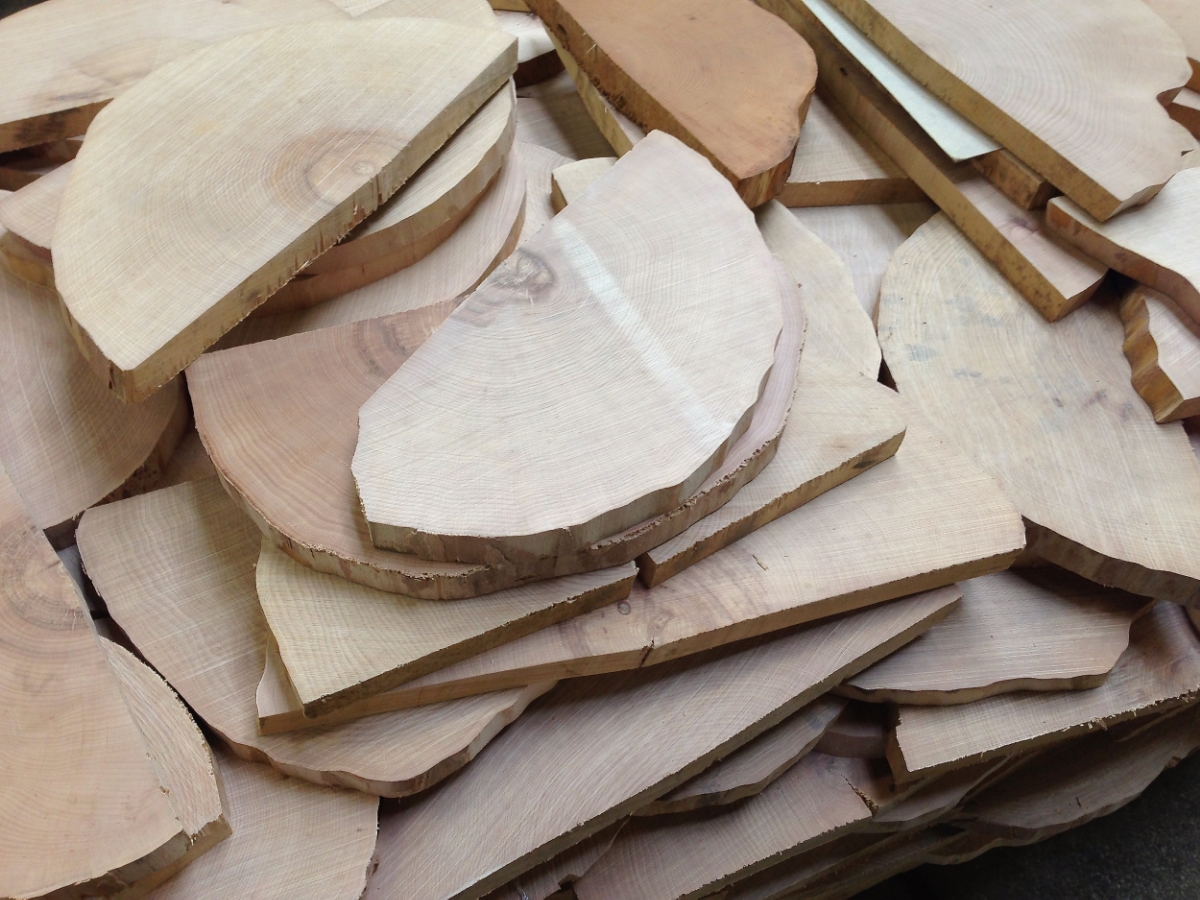
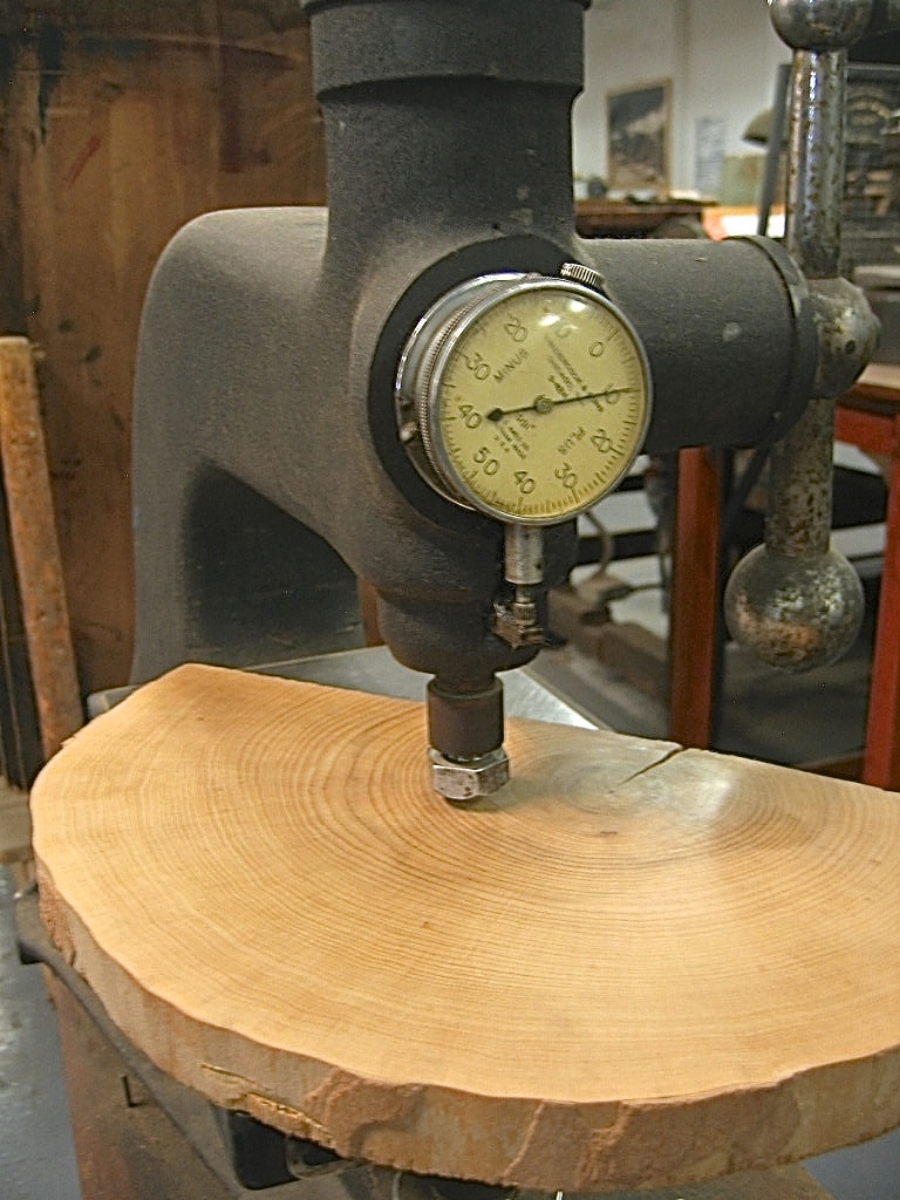
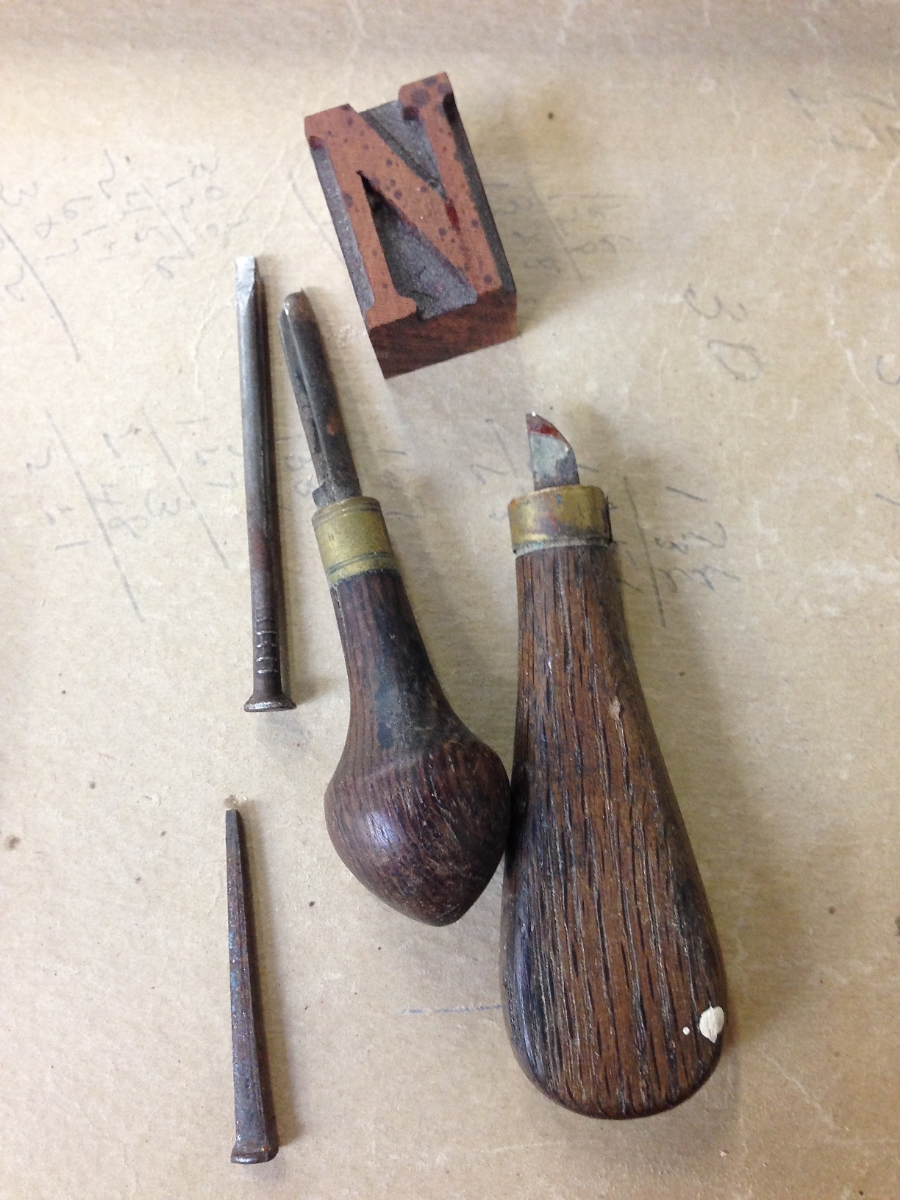
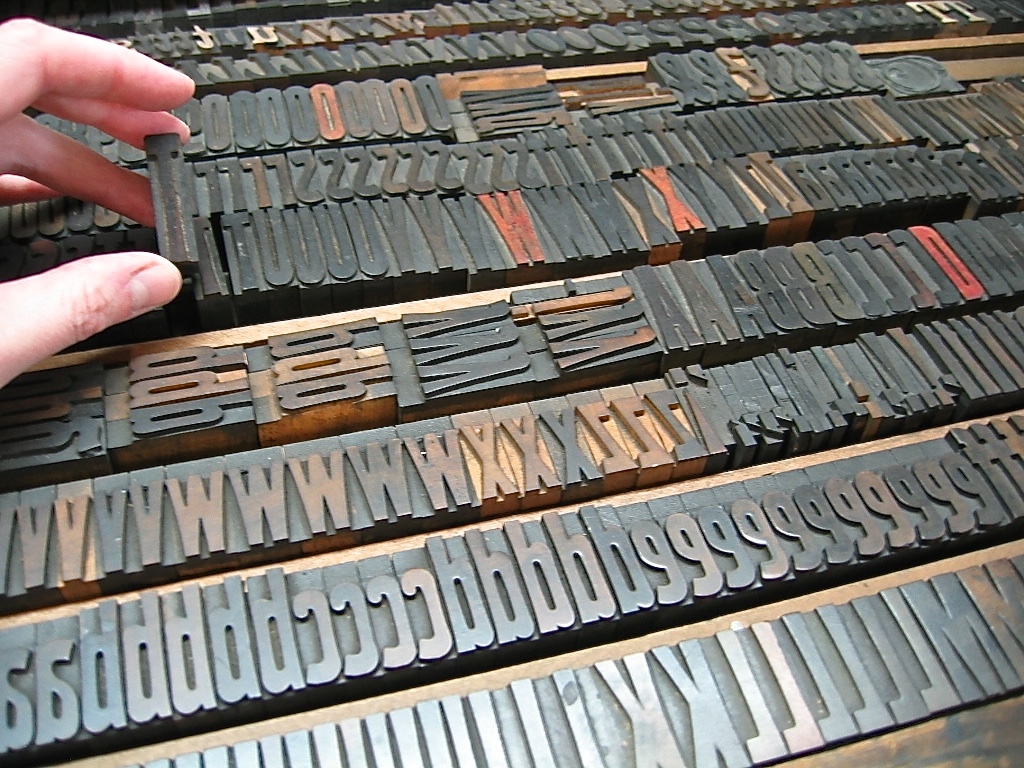
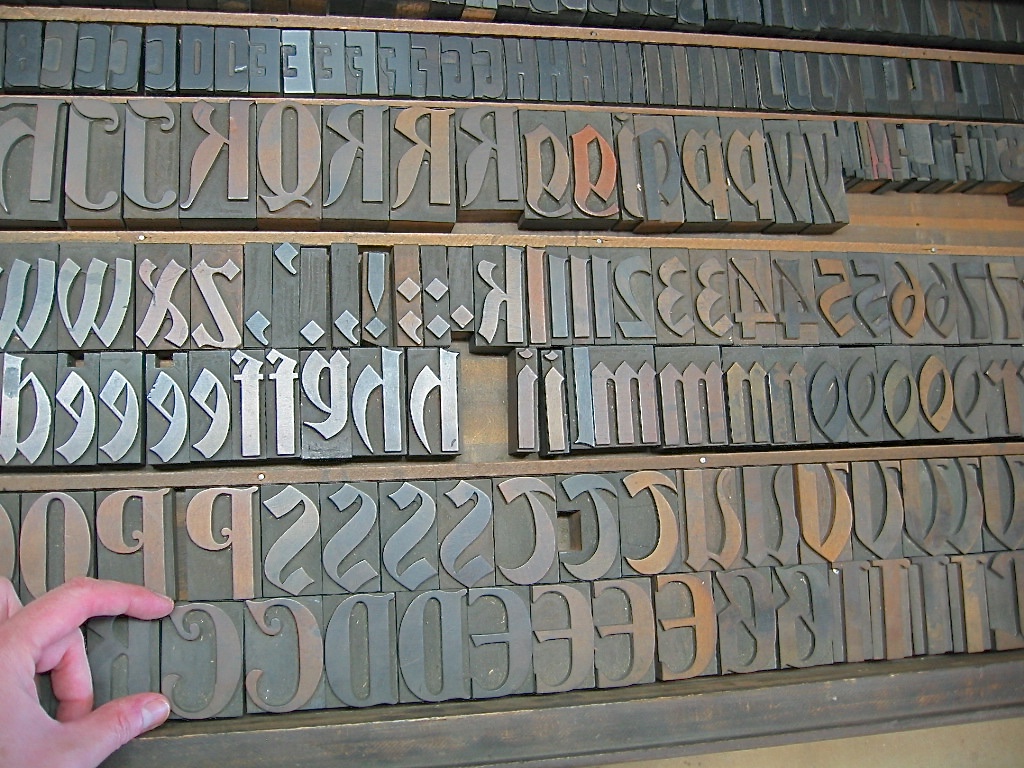
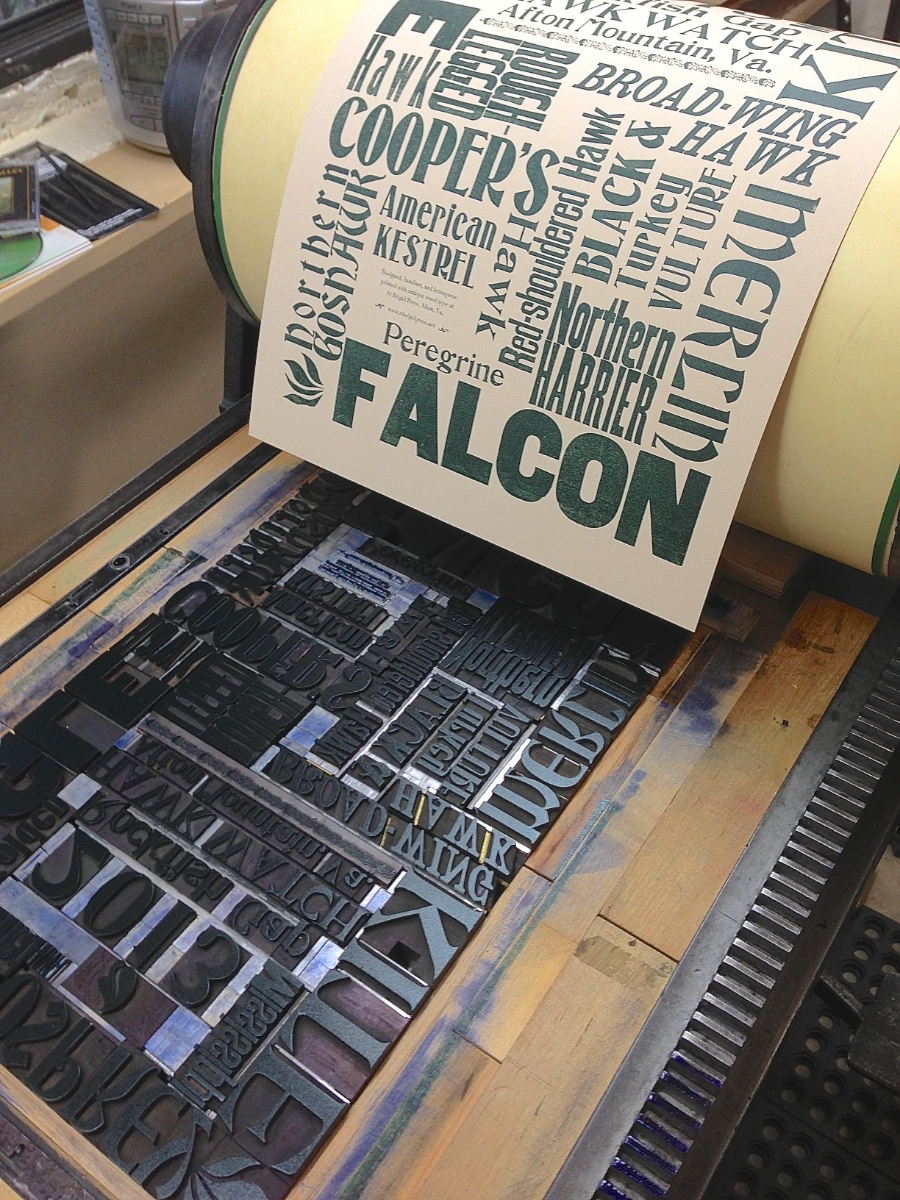
A lot of vintage type, however, either went to the scrap heap decades ago, is just too damaged to print well anymore, or is too scarce and expensive for most printers to purchase. Thankfully, there are a few excellent folks who are making brand new type from wood today!
Here is a great interview (4 mins) of Geri McCormick of Virgin Wood Type (Rochester, NY), by Frank Romano.
And another great short (1 min) video of Scott Moore, of Moore Wood Type (in Ohio), making new wood type:
Want to know more about the wonderful world of wood type?
Here are some great resources ~
- Hamilton Wood Type and Printing Museum
- “What is Wood Type?” ~ An excellent intro on Hamilton's website.
- My own photo-tour of Hamilton Wood Type Museum (in Two Rivers, Wisconsin) ~ https://flic.kr/s/aHsjzfHez3
- The Rob Roy Kelly American Wood Type Collection
- Wood Type Research
- The Art of Wood Type, by Greg Ruffa
- Moore Wood Type ~ Pantograph & Laser Cut End Grain Maple Type
- Virgin Wood Type ~ Wood Type for Letterpress Printers
Thanks for joining us on this journey into type! Please sign up below for more occasional dispatches from letterpress land!
St Brigid Press